RACKING MAINTENANCE
Keeping your storage equipment in good working is essential for creating a safe environment, meeting your legal obligations and your business running efficiently. Racking maintenance should never be taken for granted. After all, your racking may appear only as a simple steel frame but in reality, it is providing a crucial job of potentially holding tonnes of material safely above the heads of your employees. Suddenly the need to ensure it is working correctly becomes ever more important.
It is inevitable that your racking systems will be subjected daily to knocks, bumps, wear and tear, and adopting an appropriate maintenance regime is key.
Racking damage and how to prevent serious accidents
Racking systems are vital for efficient warehouse storage and operations. Not only are they a big investment, but they are also used extremely often every day. This makes them vulnerable to being hit by moving vehicles and pallets.
What are the main causes of racking collapse?
- Racking incorrectly installed
- Impact from material handling equipment
- Overloaded pallets and beams
- Racking reconfigured and not re-inspected for safety



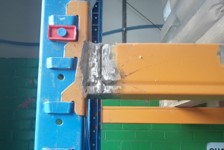
Racking damage is usually categorised into three levels of risk
According to the SEMA code of practice, racking damage is either RED, AMBER, or GREEN risk.
Red Risk
Categorised as very serious damage requiring immediate action.
- Situations where a critical level of damage is identified
- The racking should be immediately offloaded
- The racking should be isolated from future use until repair work is carried out
- Repair work usually involves replacement of the damaged component
Amber Risk
Categorised as hazardous damage requiring action as soon as possible.
- The area where damage is significant to warrant redial work, but doesn’t require immediate offloading
- Once the load is removed from a damaged component, it should not be reloaded until repairs have been carried out
- Isolate the rack following offloading to prevent use until repair work is carried out
- Repair work should be carried out within 4 weeks, otherwise, the damage is re-categorised as red risk and immediate action is required
Green Risk
Categorised as requiring surveillance only.
- Does not require a reduction in the rack carrying capacity or immediate repair
- Considered safe and serviceable
- Should be clearly identified for specific re-examination at future inspections
- Exceeding this level should be considered a risk to the racking system
Different types of damage and repair
Upright Damage & Repair
Racking front and rear uprights are often impacted by MHE.
Key things to know:
- Bends or twists can compromise the load capacity of the whole racking system
- Deflections forward or backward should be no more than 3mm before needing repair
- Deflections sideways should be no more than 5mm before needing repair
- Repairing uprights by welding replacement sections compromises the safety of the system
REPAIR: It’s advised that damaged racking uprights are replaced rather than repaired to ensure safety compliance.
PREVENT: Most damage occurs within the first 600mm of the upright. Protect racking uprights from being damaged in the first place. Protection guards deflect and absorb impact before it can cause damage to the upright.

Bracing Damage & Repair
Bracing and frames can be hit by moving pallets
Key things to know:
- Bracing can become torn or bent, compromising the load capacity of the racking.
- Damage can reduce the capacity of the frames to withstand accidental frontal impact.
- Deflections should be no more than 10mm in either direction before needing repair.
- Deflections under 10mm should still be monitored and reassessed at the next inspection.
REPAIR: Replace or repair damaged bracing as soon as required by the SEMA code of practice.
PREVENT: Although sometimes unavoidable, protecting racking frames with impact protection barriers can help reduce how close MHE can get to the racking. Training operators on careful and accurate placement of pallets can also help prevent damage.

Beam Damage & Repair
Beams can be hit when loading pallets and MHE turning in aisles
Key things to know:
- Damage most frequently occurs on the first level
- Unstable beams result in unsecure pallet loads, creating a safety issue
- Beams have a deflection tolerance when loaded that should disappear when unloaded
- Deflections showing when unloaded should be within the safe limit for that beam
REPAIR: Replace damaged beams above a category green risk to ensure your racking is safe and operational.
PREVENT: Ensure the correct beam is being used for your storage needs and regular training is given to operators to reduce the number of beam impacts.

Base Plate Damage & Repair
Base plates are essential components for the safety of racking
Key things to know:
- All racking should be fixed to the floor using 1 or more bolts per base plate.
- Unsecured racking is more vulnerable to collapse from impact.
- Damage to base plates can often cause damage to the floor.
REPAIR: Damaged base plates should be repaired or replaced as soon as they pose a safety risk.
PREVENT: Ensure all base plates are secured to an unbroken floor with at least 1 bolt. Protect MHE from hitting uprights and base plates with racking protection guards.
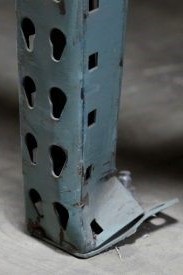
Beam-End Connector Damage
Beam end connectors are prone to knocks and tears
Key things to know:
- Beam end connectors should show no signs of cracking.
- If there are any signs of deflections, unload the beam and seek advice from your racking supplier.
- Attempting repairs by untrained staff can compromise the load capacity of the beam and the safety of the entire rack.
REPAIR: Damaged beam end connectors often result in a replacement of the entire beam to preserve the safety of the racking system.
PREVENT: Regular inspections of the system, professional repairs, and skilled operators can all help reduce the risk of beam-end connector damage.

Rust and Corrosion
Rust and corrosion can seriously weaken racking
Key things to know:
- Rust and corrosion weaken racking components, compromising safety.
- All steel will eventually corrode over time.
- Racking typically rusts when exposed to moisture for long periods.
- Paint or rubber coatings can help slow down corrosion, but can also mask issues as well as require maintenance.
REPAIR: Monitor cases of rust and corrosion, replacing all components that pose a safety risk.
PREVENT: Store components inside and away from moisture. Choose racking made from galvanised or stainless steel to slow down any corrosion.
